Steel is amazing, it is versatile and it is everywhere. Our home, at work, our free time and leisure activities are dependent on steel. Steel is the most common man-made material on the planet, and with 6 million people working in the industry and many economies based upon it, the entire world is now reliant on this alloy. Although today steel is taken for granted, it is a comparatively new product and not as old as most people imagine.
Steel derives from iron ore, and iron works have been traced back to Armenia, in fact as far back as 3,500 BC. It was not long before the use of iron spread and it soon became a staple, universal material for thousands of years. It wasn’t until 1856 that a process was perfected to produce the alloy that we know today as steel. The process of creating steel alloy is known as the Bessemer process, named after its inventor, Englishman Henry Bessemer.
Producing Steel
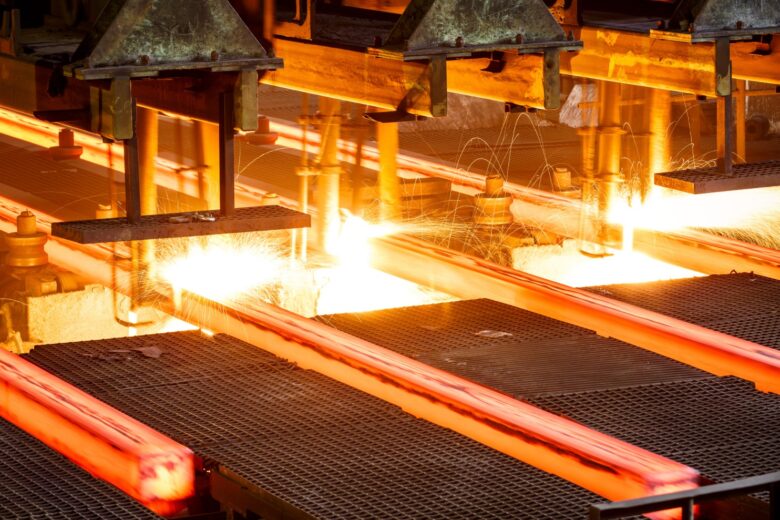
Source: mfgtalkradio.com
Henry Bessemer perfected a process whereby iron was brought together with carbon, manganese, silicon, phosphorus, sulpher and oxygen to produce an alloy. The name steel is in itself very apt. The word ‘steel’ has ancient Germanic origins meaning ‘to be strong and standing firm’. Since 1856, further derivatives of steel alloy have been developed, notably in 1913 Englishman Harry Brearley produced ‘Stainless Steel’ through the addition of chromium to the basic steel alloy.
Today there are several variations in the processes of steel production, but they are all based around one of two basic methods. The first method used, and still used today, is the blast furnace-basic oxygen furnace, or BF-BOF. Towards the latter part of the 19th century the electric arc furnace, or EAF, was introduced. The EAF method is predominantly used for the reconstitution and recycling of scrap materials.
Once steel has been produced there are a plenty more processes that it may undergo in which it is formed to suit the plethora of applications for which it is to be used. Check out the selection of steel stock at FastMetals which covers a variety of applications. Although through the production and processing of steel many different procedures will be employed, there is one constant throughout, industrial fans.
Quite simply, without industrial fans there would be no steel. There are too many applications in which industrial fans are a vital component to list, but a few of these are, Fume aspiration and filtration systems, extraction and conveyance of airborne toxins, aspiration and filtration of solid particle pollutants, de-dusting of rolling mills and brushing apparatus, galvanizing and plating systems, drum cooling and numerous cleaning and drying procedures.
By-Products
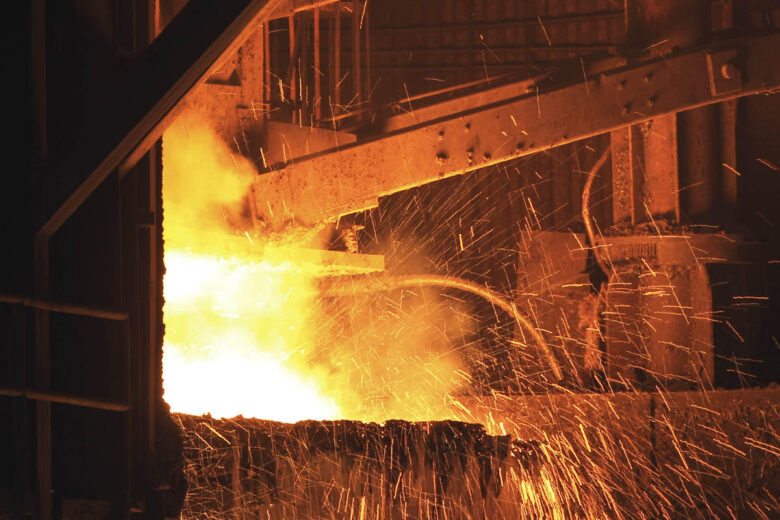
Source: cio.com
Steel is a heavy industry requiring masses of energy in numerous different forms. An enormous volume of material needs to be moved and processed. Through automation and technological advances, the industry has become less reliant on manual labor. But for those that do work within the industry it remains potentially hazardous. Not least of these hazards is the production of gasses that the process produce, in particular, hydrogen, methane and carbon monoxide.
The control and extraction of these gasses is vital to maintain a safe working environment. In order to filter out these harmful gasses, industrial fans, both axial and centrifugal dependent on the application, are employed. Although the gasses are potentially harmful and must be removed with ultra-efficiency, they are in fact a very useful, free by-products of steel production.
Industrial fans are used in the extraction, filtration, conveyancing of the gasses and aid in their storage for more purposeful disposal. These gaseous by-products can then be disposed of as an alternative source of efficient power generation. This not only has obvious economic benefits, but there are also environmental gains. Extracted gasses from steel production can also be used as fuel for engines which reduces CO2 emissions and helps to conserve natural resources.
A Safe Working Environment
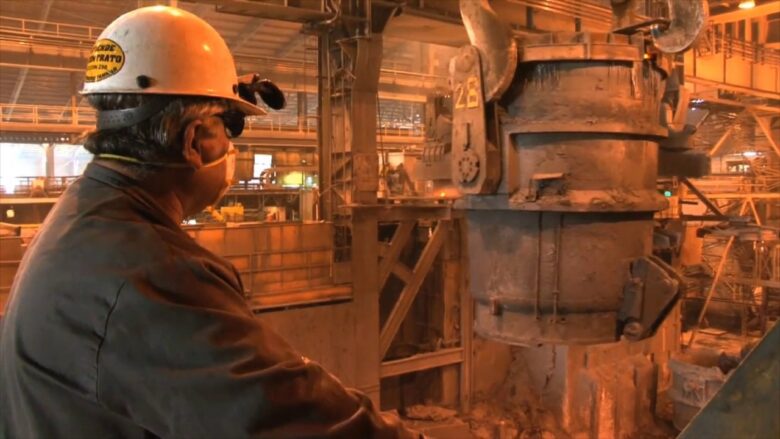
Source: youtube.com
Every industry today is acutely aware of the need to safeguard their workforce, through both their moral and legal responsibilities. Today workers have rights, they have the right to work in an environment that is safe and conducive to their overall wellbeing. There are systems for safe materials handling and to maintain air space quality, and we know that industrial fans play a key role in achieving this.
Reliable and efficient oil mist abatement systems are essential, as is the environmental air treatment within the workplace, all of which a driven via industrial fans and blowers. To maintain the set standards of safety, there requires monitoring. Once again industrial fans have a vital role to play in aiding the laboratories which constantly monitor and assess air space quality to ensure the set standards are met.
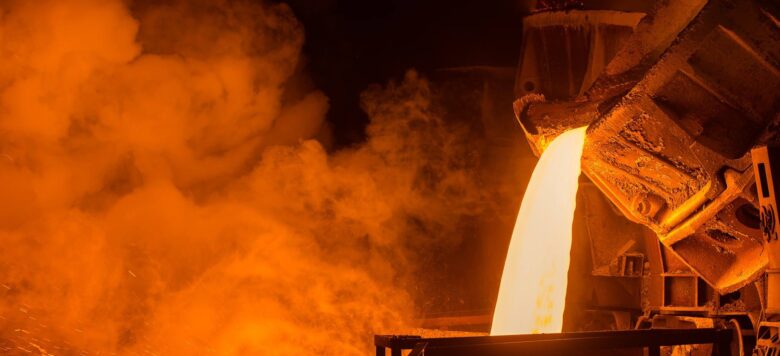
Source: bhp.com
Gaseous and solid particle air pollutants are a constant threat to the airspace in the working environment and must be constantly monitored. This is done by extraction of air samples for laboratory testing. To achieve this high quality industrial fan units, that can eliminate other outside contaminants, are used to collect air samples for laboratory testing. Without these fans accurate testing of the airspace quality would be impossible.
From production to processing, the health, safety and wellbeing of the workforce and the preservation of the environment, industrial fans play an important part in the world of steel. Indeed, we have much to be grateful for after Henry Bessemer invented steel, it is no exaggeration to say that, today, our whole lives are built upon it. And, the industry itself, which has grown immeasurably since 1856, has much to be grateful for too, and it owes its gratitude to the industrial fan. Click here for more information about industrial fans.