In the fast-paced world of industrial construction projects, time is often equated with money. Delays can lead to increased costs, missed deadlines, and unsatisfied clients. Whether you’re a seasoned project manager or a budding construction entrepreneur, streamlining the construction process without compromising on quality is the ultimate goal.
In this blog post, we’ll delve into actionable tips and strategies that can significantly accelerate your industrial construction projects, ensuring they’re completed efficiently, on time, and within budget. Read on to discover how you can revolutionize your approach and set new benchmarks in the industry.
Industrial construction projects have an established deadline that must be met; delays can cost the contractor and customer money in various forms. Project delays often arise from improper planning, insufficient materials, labor shortages, or unpredictable weather. Luckily, many techniques exist that can speed up industrial construction projects.
ALICE Technologies provides the solutions for your next industrial project; click here to learn more.
Utilize construction optioneering solutions
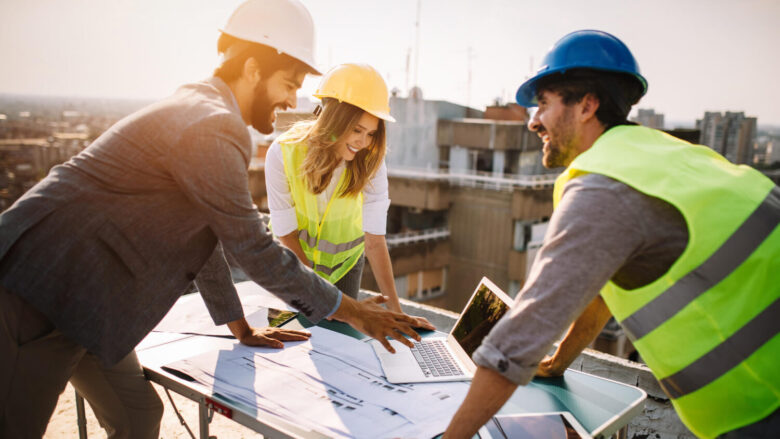
Source: build-review.com
Construction optioneering is a strategic approach that uses digital tools and data analytics to simulate different construction scenarios and determine the most efficient and cost-effective options.
Here’s how it can expedite the construction process:
- Improves decision-making: Optioneering empowers stakeholders to make informed decisions in the early planning phases. By simulating different scenarios and outcomes, teams can identify potential issues and opportunities, reducing the time spent on rework and corrections later in the project.
- Enhances resource management: Optioneering can optimize resource allocation by leveraging data analytics. This includes efficiently scheduling staffing, machinery, and materials, significantly reducing downtime, and expediting project timelines.
- Reduces uncertainty and risks: Through predictive modeling, optioneering aids in foreseeing potential risks and uncertainties that could hinder the construction process. Early identification and mitigation of these risks prevent delays, ensuring the project stays on schedule.
- Facilitates agile execution: Optioneering enables a flexible and responsive approach to construction. If unforeseen changes occur, teams can quickly reassess and adapt their strategies, minimizing potential time losses.
By integrating construction optioneering into the project planning phase, industrial construction projects can achieve more efficient workflows, better resource management, and faster project completion.
Use a 3D model to calculate your QTO
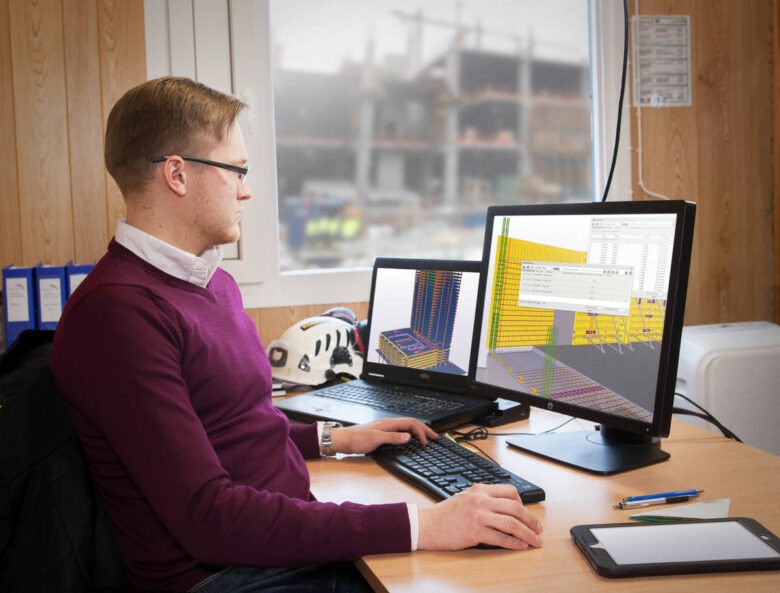
Source: tekla.com
Utilizing 3D models makes it easier for everyone on a project team to visualize a realistic representation of the finished product.
Furthermore, cloud-based 3D modeling encourages greater communication and coordination by allowing everyone at once to access the visualization from anywhere around the world – making collaboration faster, more accessible, and more efficient.
3D modeling elevates the quantity takeoff (QTO) process – an essential element in construction planning that entails estimating the required materials. Traditionally, QTOs were calculated manually, a time-consuming and error-prone process. With 3D modeling, the QTO is faster and more accurate.
Use prefabricated components or modular systems
Prefabrication involves building components offsite to reduce construction time on site. This may take the form of panels or modules transported directly to the construction site for assembly. Prefabrication provides several advantages, including improved precision and decreased weather-dependency.
Offsite work also eliminates the need for heavy machinery on construction sites, helping reduce noise pollution and safety concerns while eliminating staging materials, which create clutter and slow work processes.
Use temporary structures during demolition phases
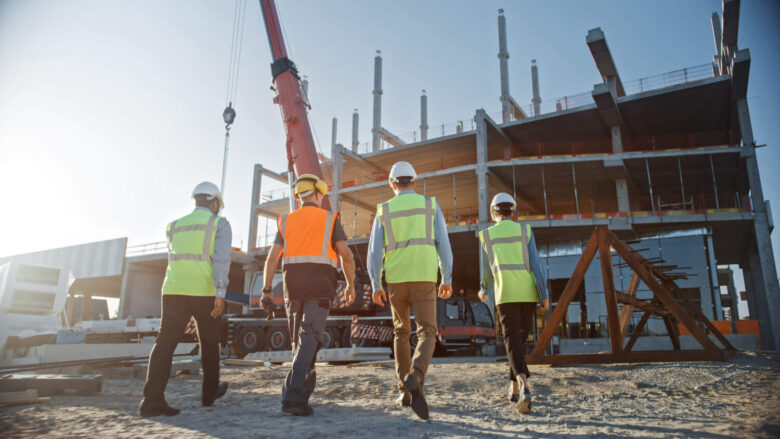
Source: mhwilliams.com
Using temporary structures during the demolition phases can tremendously expedite industrial construction projects. Temporary structures such as scaffolding, props, and shoring systems provide crucial support for safely and efficiently removing existing structures. They can stabilize unsafe sections, prevent collapses, and ensure smooth, controlled demolition.
Additionally, temporary structures can house essential equipment and materials on-site, ensuring they are readily available when needed. This accessibility can significantly reduce downtime associated with transporting machinery or resources to and from the site, keeping the project on schedule.
Employ just-in-time management
Just-in-time (JIT) management is a production strategy that seeks to improve a business’s return on investment by reducing in-process inventory, associated carrying costs, and minimizing production times.
Even though JIT management originates from the Japanese manufacturing industry, it can be applied to industrial construction projects to optimize efficiency and speed. Here’s how JIT management can speed up industrial construction projects:
- Reducing inventory costs: JIT management operates on the principle of having materials delivered ‘just in time’ for use. This means materials are not stored on-site for extended periods, reducing storage costs and the risk of damage or theft.
- Minimizing waste: Materials delivered as and when needed ensure fresh supplies, reducing waste due to spoilage or damage, as commonly seen in construction projects.
- Streamlining production: With JIT, tasks are often organized continuously, allowing a smooth transition between different project stages.
- Improving quality: JIT strategy often necessitates close relationships with suppliers to establish timely delivery of quality materials, thereby improving the overall quality of the construction project.
- Increasing flexibility: JIT allows for more flexibility in dealing with changes or problems during construction. For example, if a flaw is discovered or the customer changes their mind about certain aspects of the project, JIT management allows for quick adjustments due to its flexibility in scheduling and smaller batch sizes.
Technology Integration: The Cutting Edge
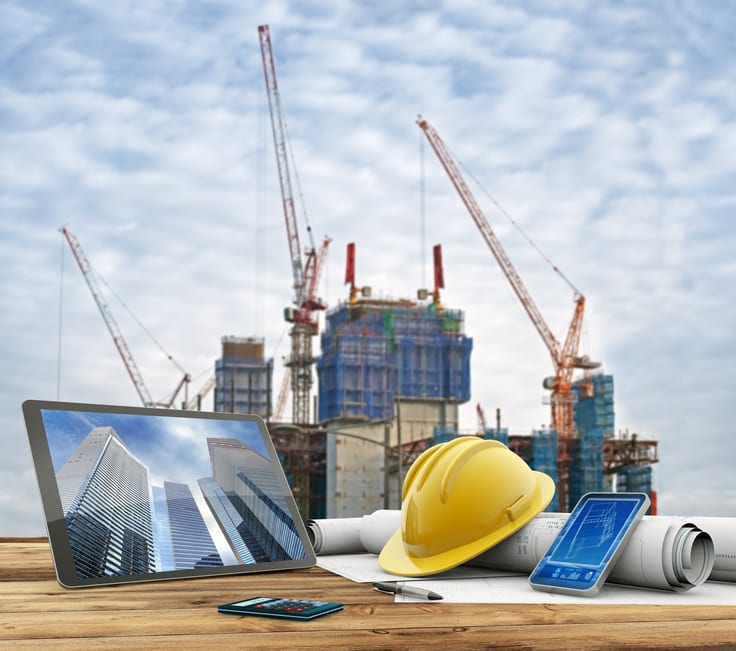
Source: procore.com
In the rapidly-evolving construction sector, technological advancements are not just luxuries; they’re necessities. With Building Information Modeling (BIM), a digital representation of a construction’s physical and functional characteristics, project visualization and management have been revolutionized. It allows seamless collaboration among different stakeholders, ensuring every detail is accounted for.
Meanwhile, drones have transformed the way site inspections are conducted. No longer confined to ground-level observations, these aerial devices capture comprehensive views of construction sites, aiding in accurate site assessments and progress evaluations. Their bird’s-eye view ensures no detail, however minuscule, is overlooked.
Enter the Internet of Things (IoT) devices, the silent watchdogs of the construction process. By embedding sensors in machinery and materials, data collection becomes real-time. This not only aids in proactive maintenance but also in monitoring material usage, ensuring efficient resource allocation.
Speeding up your industrial construction project is easy when you use these tips
The conscious implementation of modern methodologies and innovative technologies can greatly enhance the efficiency and speed of industrial construction projects.
From the precision of 3D modeling and QTO, the practicalities of prefabrication and temporary structures, to the strategic implementation of JIT management and construction optioneering, the industry has numerous avenues to streamline operations.
By embracing these advancements, stakeholders can expedite projects and improve quality, reduce costs, and minimize risks, paving the way for a more robust and resilient construction industry.