Zero defects is a term “Absolutes of Quality Management” and the concept mentioned in the book has emerged as proper and mostly recommended for quality management.
It is so highly regarded that even six-sigma is adopting it as one of the major theories. But this concept is lacking in criticism and unfortunately, most of the belief that zero defect in quality management is just next to impossible.
On the other side, the majority of the people have worked hard on this concept and proved the naysayers wrong. They convinced the non-zero defects believer by pointing out that zero-defect doesn’t mean complete perfection but it’s about eliminating the waste, as well as the majority of the defects, can be reduced in this way.
Hence, zero defects don’t mean perfection, but it is about ensuring the highest in quality standards. In this article, we have discussed whether zero defects in quality management are possible or not. But before we dig into that, just have a quick look at what is zero defects, its theory, and its pros as well as cons.
About Zero Defects
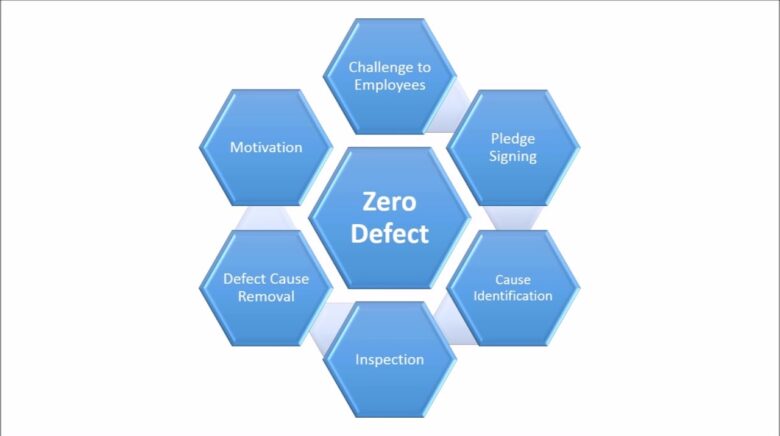
Source: youtube.com
Zero defects in quality management are logically not possible but in this scenario, we are not talking about complete perfection. On the exact note, the organizations are looking forward to reducing all the possible defects and meet the quality standards.
As per the definition given by six sigma, zero defects mean 3.4 defects per million opportunity and allowing for sigma process shift that is 1.5 approximately. Hence, zero defects should be viewed as a quest for perfection to meet quality standards by avoiding unwanted defects.
Now, let’s take a look at how zero defects can be beneficial, on what theory it is based on.
About Zero Defects theory
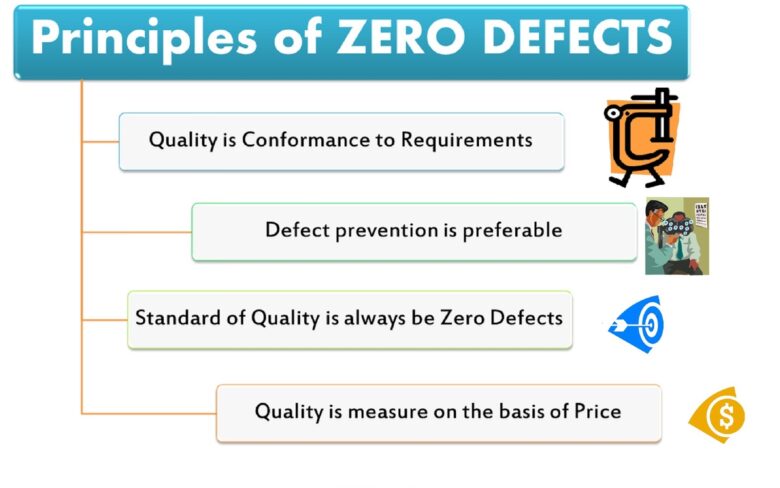
Source: shakehandwithlife.in
The theory of zero defects has been based upon four elements that are as followed:
- Performance – The performance is judged by the quality standards and zero defects seek perfection as close as possible.
- Requirement – Quality should meet the requirement and introducing zero defects in this means providing quality requirements at a particular time.
- Step-by-step procedure – In zero defects procedure, the quality is looked after from the beginning to the end.
- Measurement in financial terms – Later, at the end of the procedure, one need to judge production, waste as well as revenue regarding budget impact.
The most important feature of zero defects is the process of elimination of waste. It eliminates any of the unproductive processes, employees, as well as tools that do not add value to the project. Now, let’s have a quick look at zero defects’ pros and cons.
About Zero Defects Pros And Cons
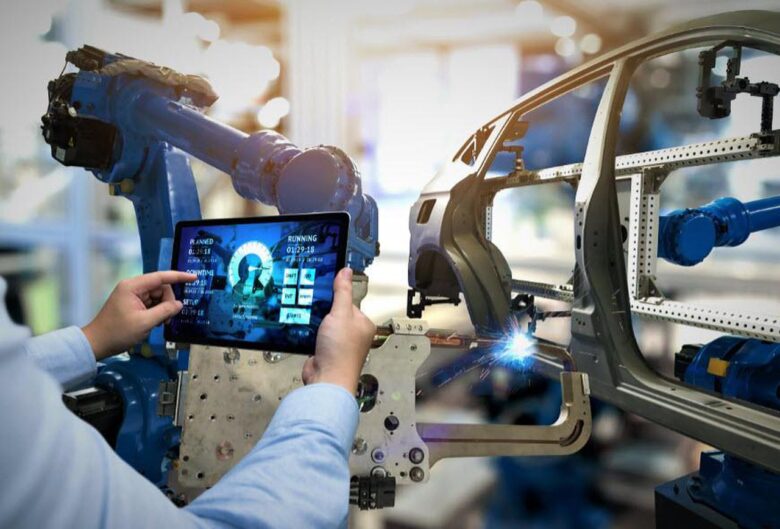
Source: techiexpert.com
One of the most clear-cut advantages of zero defects is the deduction of defective level in the project which also saves money and meets the requirement of the customers. These steps would also lead to better sales and profit in a short time.
On the other hand, it may be possible that the team gets misguided or have a different outlook on the definition of zero defects. Having zero defects in quality management is not possible and if the team kept looking forward to getting completely zero defects, then they would waste their time as their satisfaction wouldn’t meet.
Now, let’s have a look at is six-sigma zero defects standard or not.
About Zero Defects concept in six-sigma standards
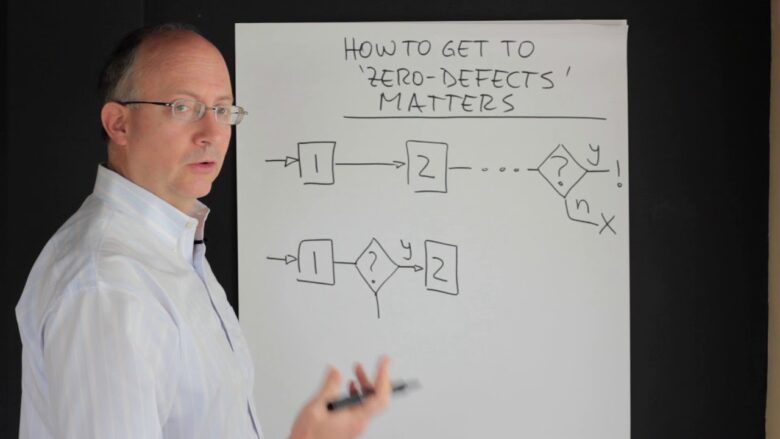
Source: youtube.com
Currently, six-sigma has amazed all their customers by their stunning quality standards and it seems that zero defects concept has made the quality management of six-sigma better than ever. Talking conceptually as well as fundamentally, zero defects and the six-sigma walks on different lines; let’s have a quick look to it:
- Even kid would explain about zero defects but when it comes to six-sigma, one must have a particular knowledge regarding some of the mathematical as well as statistical concepts.
- Zero defect completely focuses on how to prevent defects whereas six-sigma focuses on how to manage defects. Six-sigma does focus on the deduction of defects but dealing with zero defects, it reduces the occurrence of the defects.
- The training of zero defects and six-sigma is different as well. In zero defects, not special training is provided as it just focuses on the delivery of the usual training. Whereas the six-sigma has particular sets of training to be followed. Even it includes various certification levels such as green belt certification and yellow belt certification.
- Talking about the concept of zero defects, it aims to have a reduction of defects as much as possible. This can be achieved by working right for the first time and thereafter as well. Whereas in six-sigma, the concept is based on 3.4 DPMO and this also seems to very few defects. Hence practically, zero defects in quality management cannot be achieved.
- In zero defects there’s no need for extra employees. But when the company calls for rigorous implementation regarding six-sigma, then it requires six-sigma green belts as well as six-sigma black belts. To avoid this disadvantage, the company consists of training resources internally.
- Talking about the standards, the zero defects have way high standards as it does not allow single defects at all. But in six-sigma, few defects that is 3.4 are accepted in a million opportunities. This is quite easy to know but performing implementation and detecting the defects is way harder.
- Coming to the hot topic of all time, employee involvement. In zero defects, each employee is being involved in the definition and works for fixing the possible defects. Whereas, in six sigma, not all the employee is given equal importance as all employees cannot handle the six-sigma statistical mastery.
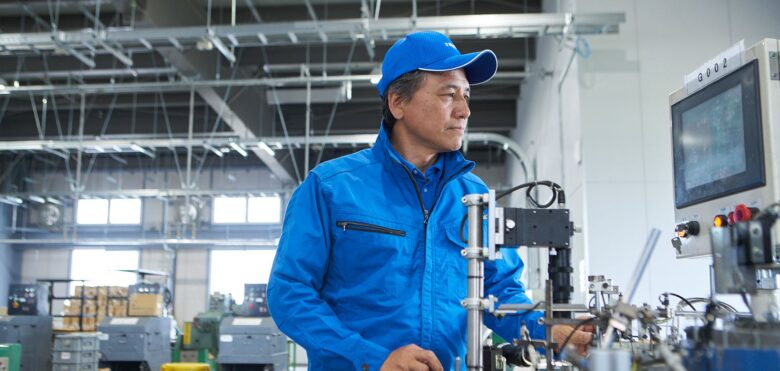
Source: mizuki-corp.co
Hence, you may have concluded from the above points that zero defects is much demanding compared to six-sigma. Not every company can meet the quality standard as six-sigma has. It took a lot to invest to achieve quality standards.
Moreover, if you are willing to go forward for six-sigma then do go through its six-sigma green belt certification as well as yellow belt certification. Currently, quality management is highly demanded. So, what are you waiting for, go and give a shot to this one if you are interested?
Hence, the above was everything you need to know about zero defects in quality management. Zero defects in quality management are possible, only if you know zero-defect definition well. It’s not at all about perfection but close to perfection as much as possible.