Rubber feet and bumper are items that we commonly use in our lives, but in most cases, we are not aware that they are part of our day to day life. They are used on both the exterior and the interior, and they protect our furniture, chairs, and floors, and they can prevent scratches, dents, and bumps.
When you use these small items, you will reduce the sound the furniture makes, you won’t risk your items slipping and falling and in vehicles, they are used to absorb the shock. There are a lot of different shapes and sizes that feet and bumpers come in, and here we are going to talk about the technology and the manufacturing process. Continue reading if you want to know more about how rubber is produced and how it is processed later on, so we can get items that will make our lives better.
Where does the rubber come from?
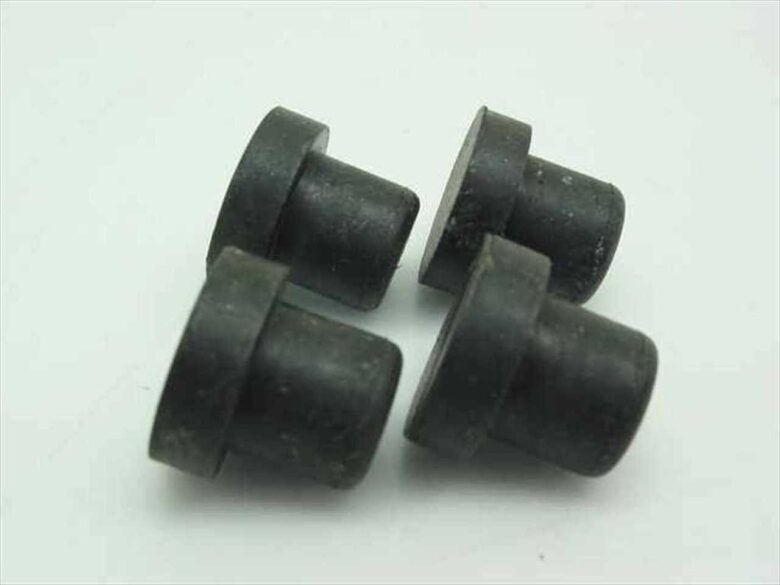
Source: recycledgoods.com
As you already know there is the natural material and the synthetic one. Here we are going to give you some inside of the procedure of how latex is obtained, and later on, how synthetic rubber is made.
The first thing you need to know is that when natural rubber is used, latex is harvested from the trees that have the same name as the material. The whole process starts by cutting into the bark of the tree and the latex will flow into the cup that should be attached to the bottom of the tree.
Once the latex is obtained, experts use the operation of coagulation to extract the material we want from the latex. This procedure lasts about half a day, and at the end, a sheet with a width if one eight of an inch is made. The material is later on processed and depending on the manufacturing technology, we can get high-quality rubber or a lower quality one.
When it comes to synthetic material, several different processes are used, and the most common one is the polymerization of the molecules. With this procedure, the molecules are linked with each other and the results can vary between oil and gasoline resistant rubber up to SBD or styrene-butadiene. The whole process is relatively long and complex, and we won’t go into detail here.
Technology and Manufacturing
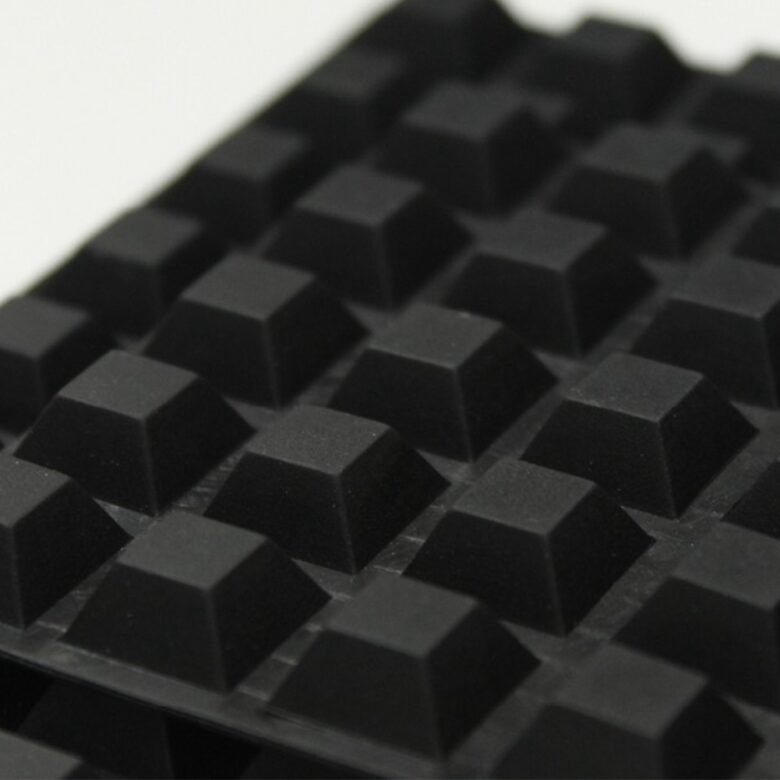
Source: shopee.ph
There are a lot of different ways to manufacture rubber, and depending on the process and the finish, there are different advantages and disadvantages to each and every one of them.
Extrusion is used to produce large quantities of the same item, and this process is probably the cheapest one. With it, the most common items that are made include gaskets, cords, and tubes. When it comes to latex dipping, this way is used to add several layers on the same product, so that it becomes thicker and more durable. Gloves, balloons, and tubes are most commonly made with latex dipping, and this is the best way to create items that have a complex shape. Calendaring is the most complex and probably the most expensive way to create items of this material. With it, you can choose the thickness of the item, and it is most commonly used to create sheets or films.
Not every technology or machines can produce rubber feet and bumpers, so when you want to produce these parts, you need to get the right devices. Now let’s talk about the exact way of how these small items are created.
According to EtolRubber.com, the most common method to create the feet and bumpers is called molding. By definition, this process includes the material being heated until it becomes liquid, and later on, it is poured into a mold of the specific shape we want to achieve.
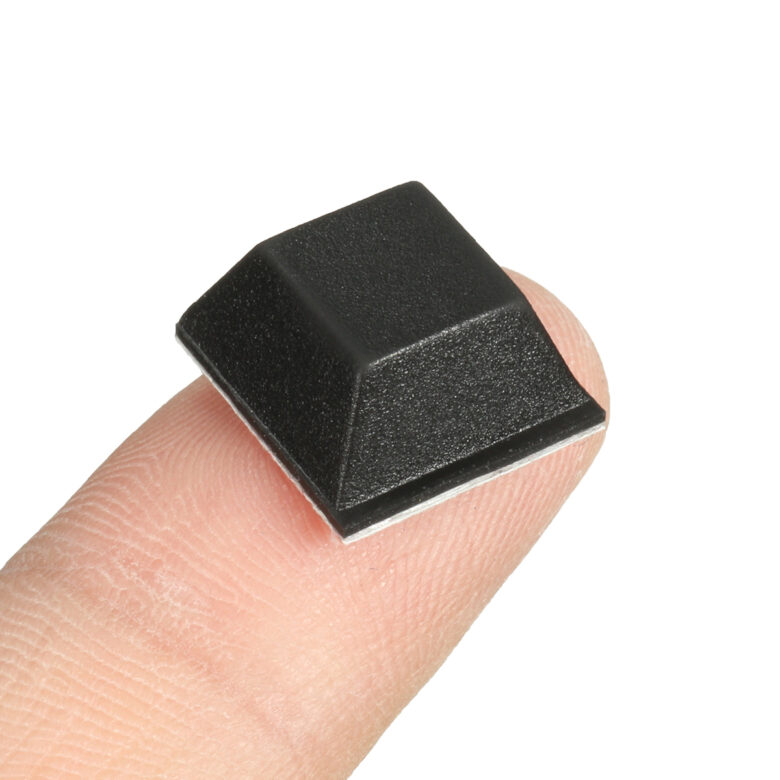
Source: ebay.com
This procedure consists of 3 different manufacturing processes and the first one is compression molding. The compression process is something that has been used for centuries and it is probably the cheapest way you can make rubber feet or bumpers. First, the compound is formed into a chunk, and then it is placed in a cavity so you can get the desired shape. This is a slow procedure so that you can end up with the exact shape you desire. Even though this is a time-consuming task, the end result will be an item that has a high viscosity and poor flow. This means that the product will be durable and you can protect anything you want with it.
The second process we are going to talk about is called transfer molding, and it was developed so that the whole procedure of the compression molding can be made better. The first thing that experts do is, they load the chamber with chunk and then the material is put in different cavities. This is done before the rubber is heated, so that the material can, later on, flow in the right places. During this manufacturing procedure, the material will fill all the cavities with ease, and more complex shapes can be created. This is a great procedure when you want to create rubber tips and chair feet. The downside of it is that is pretty expensive compared to the compression molding, and it is more complex.
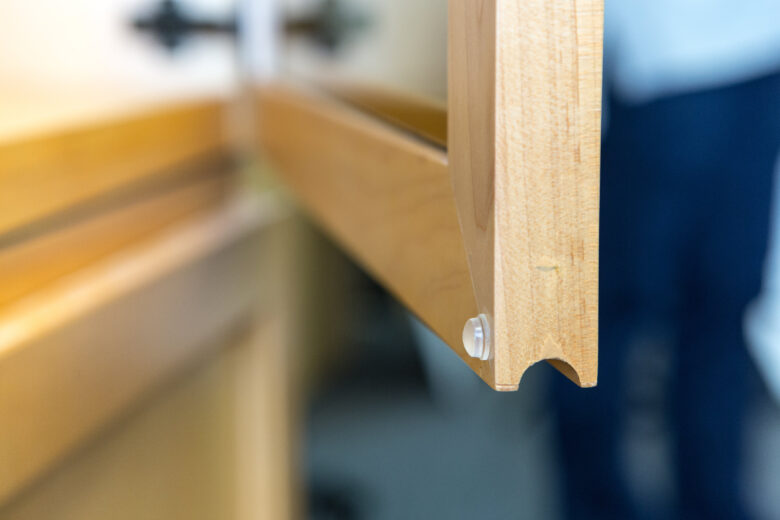
Source: bumperspecialties.com
The third way of this manufacturing procedure is called injection molding. As the name suggests, the material is injected into the mold, and then a press is used to create the desired shape. The procedure is the fastest one compared to the first two, and here you can create any shape or form, no matter how simple or complex it is. It is also the best type if you want to eliminate any errors, and if you are looking to automate the whole production.
To create feet and bumpers, there are a lot of different machines that are used, and the most common ones include bale cutters, dispersion kneaders, and hydraulic presses. The next time you want to buy these items, you can talk to the seller and ask them how the items you are purchasing were made. Now you have a better idea of the rubber manufacturing procedure and it is going to be easier for you to understand why certain items cost more than others, depending on how they were created.