Automation has been a cornerstone of automotive manufacturing for decades, driving efficiency and innovation. Today, a new generation of technology, collaborative robots (cobots), is transforming the industry like never before. Unlike traditional industrial robots, cobots are designed to work side-by-side with humans, combining precision, adaptability, and safety.
This article explores how cobots are reshaping automotive manufacturing and driving the industry into a more agile, productive future.
The Evolution of Automation in Automotive Manufacturing
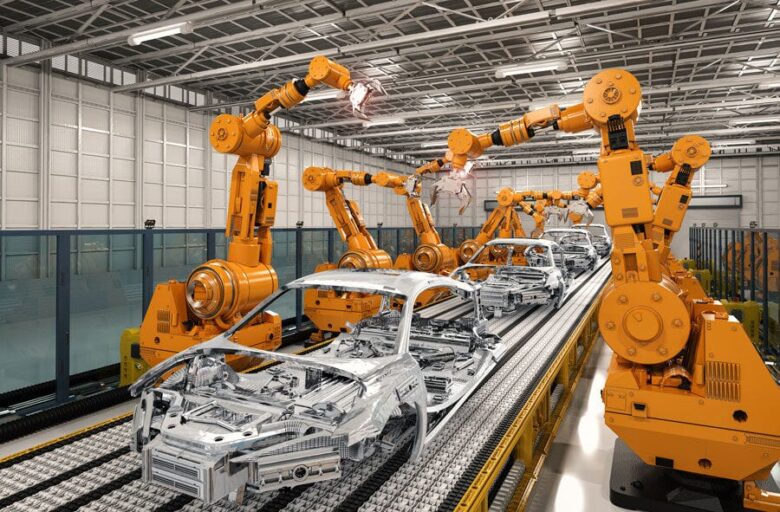
Source: cigen-rpa.medium.com
The introduction of the assembly line by Henry Ford in 1913 marked the beginning of automation in automotive manufacturing. Over the decades, the industry moved toward greater mechanization, culminating in the 1960s with the deployment of the first industrial robots. These robots were powerful but required strict separation from humans due to safety concerns, operating behind fences or in isolated areas.
Cobots emerged as a response to the limitations of traditional robots. They are smaller, more intuitive, and capable of working safely alongside human operators. Equipped with advanced sensors, AI, and machine learning algorithms, cobots adapt to their environments and perform a variety of tasks with remarkable efficiency.
Key Advantages of Cobots in Automotive Manufacturing
Cobots thrive in shared workspaces, complementing human skills rather than replacing them. For example, a cobot might handle repetitive tasks like tightening screws while a human focuses on complex assembly. This collaboration reduces fatigue for workers and ensures higher productivity and accuracy.
Safety is a critical factor in manufacturing. Cobots are equipped with sensors and AI that allow them to detect obstacles, including humans, and stop their movements to prevent accidents. This capability has helped companies meet stringent safety regulations while fostering a safer work environment.
Cobots often cost less to deploy and maintain compared to traditional robots. Their versatility reduces the need for multiple specialized machines, and their rapid deployment means manufacturers can achieve a faster return on investment. For small and medium-sized manufacturers, this affordability is a game-changer.
Cobots are inherently adaptable. They can handle various tasks, from welding and painting to assembly and inspection. This flexibility allows manufacturers to scale operations efficiently, making cobots a vital tool in an industry where customization and agility are increasingly important.
Applications of Cobots in the Automotive Industry
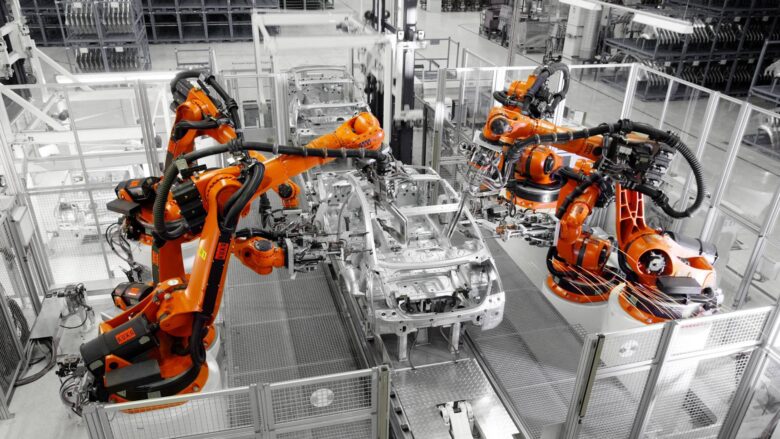
Source: kuka.com
Cobots excel at repetitive and precision-based tasks. On assembly lines, they handle jobs like welding, applying adhesives, and installing components. Their precision minimizes errors, ensuring high-quality output.
The automotive industry relies on exacting standards. Cobots equipped with cameras and sensors can inspect components for defects with unparalleled accuracy. This automated quality control reduces errors and waste, enhancing overall efficiency.
Material handling is another area where cobots shine. They transport parts between workstations, sort components, and assist with loading and unloading heavy materials. By automating these tasks, manufacturers save time and reduce workplace injuries.
Cobots are invaluable for producing custom car models and prototypes. Their flexibility allows manufacturers to quickly adapt production lines to meet specific customer demands, accelerating time-to-market for new designs.
Successful Integration of Cobots
Industry leaders such as Ford, BMW, and Toyota have embraced cobots to enhance production. For instance, Ford uses cobots for tasks like sanding and painting, which require consistent precision. BMW employs cobots to assist with component assembly, improving both speed and accuracy.
Manufacturers have reported significant improvements in productivity, quality, and safety after integrating cobots. At BMW, the inclusion of cobots reduced assembly errors by 30% while increasing overall output.
Challenges and Considerations in Cobot Adoption
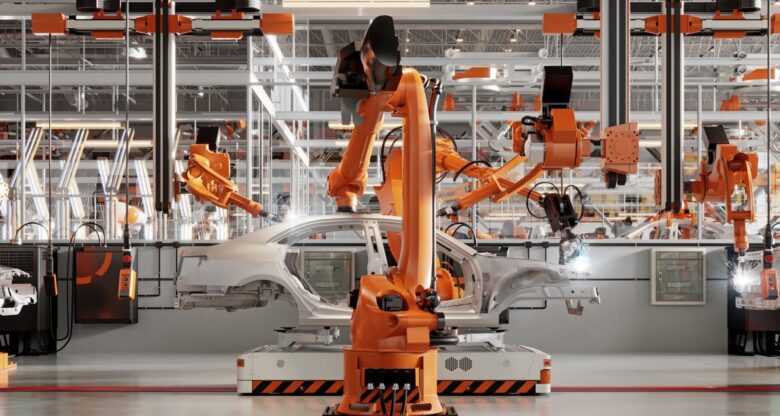
Source: knowhow.distrelec.com
While cobots are more affordable than traditional robots, the initial investment in hardware, software, and training can be significant. Smaller manufacturers may struggle with the upfront costs despite the long-term benefits.
The rise of cobots has sparked debates about job displacement. While cobots are intended to collaborate with humans, their efficiency can lead to reduced demand for certain roles. Balancing automation with job creation remains a challenge for the industry.
To maximize the potential of cobots, companies must invest in upskilling their workforce. Employees need training to collaborate effectively with cobots, ensuring a seamless integration into existing workflows.
The Future of Cobots in Automotive Manufacturing
The future of cobots lies in integration with cutting-edge technologies like artificial intelligence (AI) and the Internet of Things (IoT). These advancements will make cobots even smarter, enabling predictive maintenance and seamless communication with other machines on the production floor.
The market for cobots is expected to grow exponentially, driven by demand from industries like automotive manufacturing. Analysts predict that cobots will become a standard feature in factories worldwide, further transforming the way cars are built.
As the industry shifts toward electric vehicles (EVs) and autonomous cars, cobots will play a critical role in producing these advanced vehicles. From battery assembly to the installation of complex electronic systems, cobots are poised to handle the challenges of modern automotive manufacturing.
Conclusion
Cobots are revolutionizing the automotive industry, bridging the gap between human ingenuity and robotic precision. They enhance collaboration, improve safety, and provide cost-effective solutions for manufacturers of all sizes. As the industry continues to evolve, the adoption of cobots will be a defining factor in driving innovation and maintaining competitiveness.
By embracing cobots and other automotive robots, manufacturers can build a future that prioritizes efficiency, safety, and sustainability while remaining at the forefront of technological advancement.