The crème de la crème of the robotics industry gathered at the 2019 Autonomous Mobile Robot (AMR) Conference. The conference was powered Association for Advancing Automation (A3) and the Robotic Industries Association (RIA). It had 450 people in attendance.
The goal of the conference was to evaluate where we are in robotics development, what the challenges are, and how to progress. Subjects such as the manufacturing of AMRs, mobile manipulation, and standardization were discussed. Industry giants such as Universal Robots, Harmonic Drive, Waypoint Robotics, Precise Automation, Kaarta, and Vecna Robotics were among exhibitors. So, whether you are a custom motor manufacturer or just an enthusiast, what could you learn from this conference?
Below are six things that we learned and would like to share:
1. The Accuracy of Autonomous Mobile Robot has Improved but Differs
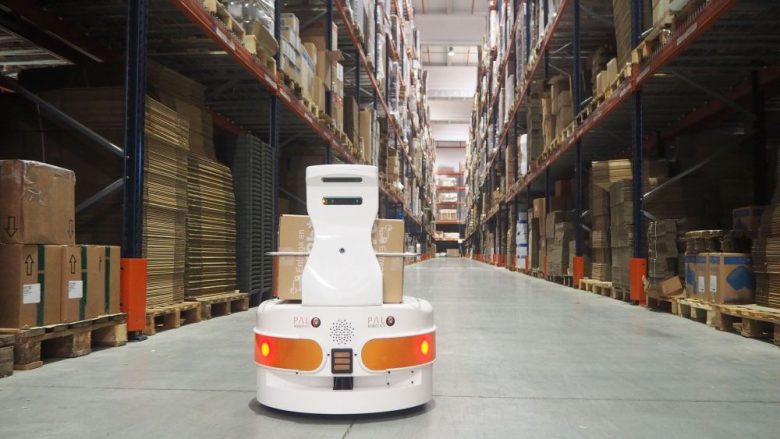
Img source: blog.pal-robotics.com
Autonomous mobile robots have a lot in common. However, the differences in their mode of operation have two significant effects: it determines safety and effectiveness in different settings. To help improve the AMR’s ability to read its surroundings, it comes with serval sensory options: odometry sensor, navigation, obstacle avoidance, object detection, and localization mapping. How accurate it’s able to navigate its surroundings depends solely on the sensor and algorithm utilized.
With the advancement in AI and machining learning, there is hope the process of remote sensing, obstacle recognition, and obstacle avoidance will improve tremendously. The addition of an AI Camera which can identify and categorize items and also interact with other robots will be a game-changer.
It is essential to improve the accuracy of AMRs: theн need more sensory features. The introduction of Vision-based SLAM (simultaneous localization and mapping) should revolutionize the industry. With it, robots will have the capability to map and categorize objects, alter their approach depending on the type of obstacle and know the right object to pick up.
2. Standardization of Safety Procedure
Currently, The U.S. Occupational Safety and Health Administration (OSHA) has no laid down safety regulation guiding the use of robotics. Notwithstanding, it is mandatory robots act by National Recognized Testing Laboratories such as UL.
The RIA has been working on the first phase of the standardization for the last four years. The first phase includes validation, requirements and protective measures, definitions, design, verification, and information for equipment use disclosed by Micheal Gerstenberger, chairperson of the RIA standards committee.
The second phase of standardization includes on-site appliance and precise requirements and regulation to autonomous mobile robot users.
3. Manufactures and Dealers Must be Acquainted their Customers
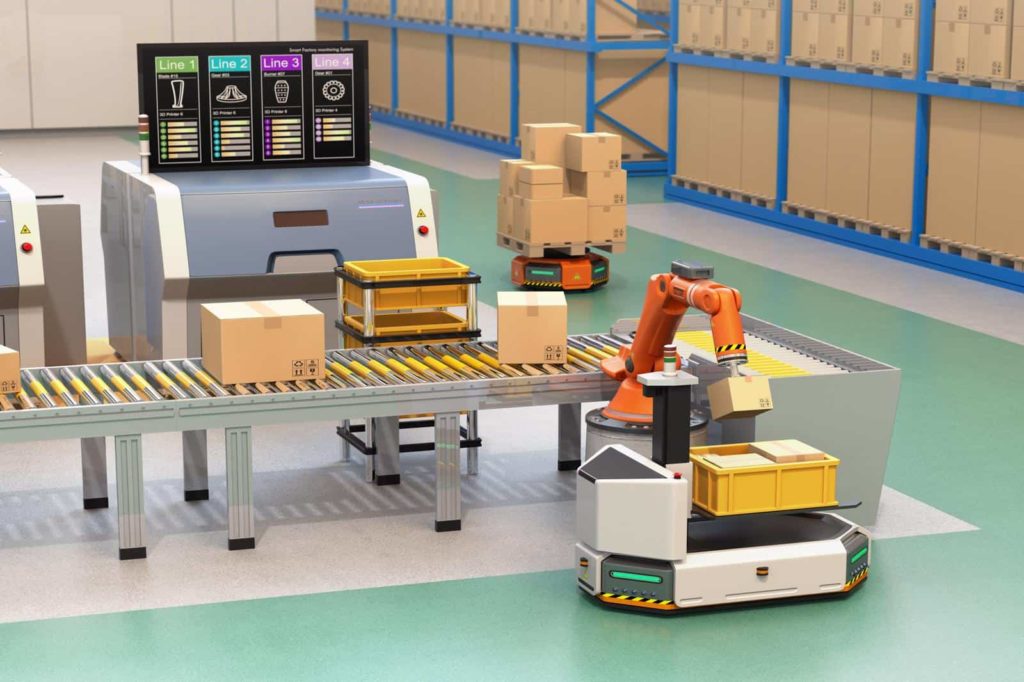
Img source: cognitionfactory.com
According to a Deloitte study, 3.4 million jobs will be available in the manufacturing sector over the next two decades. Unfortunately, about 2 million of them will go unfilled. For manufactures of AMRs, this is good news. This is an opportunity to deploy AMRs.
However, before a bottle of champagne is popped, it is important these companies get to know their customers first. Find out, if the customers can accommodate AMRs, the level of demand, can they afford it, and are they even aware of such technology.
According to Bob Doyle, vice president of the RIA and A3 Mexico, it is crucial to educate potential clients on the importance of robots and AMRs to the process of industrial automation because many of the companies that need this technology are not yet at Industry 3.0. It is also important to consider how the AMR technology will alter the consumer’s operational setup. For instance, how will it affect the company/ facilities Wi-Fi network?
Logistics is also another factor manufacturing companies need to figure out. In a world where consumers have services like Amazon Prime, their expectations will be similar- low priced, 24 hours delivery, and free shipping. This is an opportunity for manufacturers and dealers; it is also a challenge.
4. Interoperability
Denise Ebenhoech, regional head of advanced robotic applications at KUKA AG, argues that it makes no sense using one robot to resolve every supply chain difficulties since there are many robots out there designed for different applications. Why?
Well, according to her, each AMR is created for different responsibilities and can interact and collaborate with humans. It becomes imperative manufacturers and users synch to find the best AMR for every situation.
5. Mobile Manipulation is Young and its Future Looks Promising
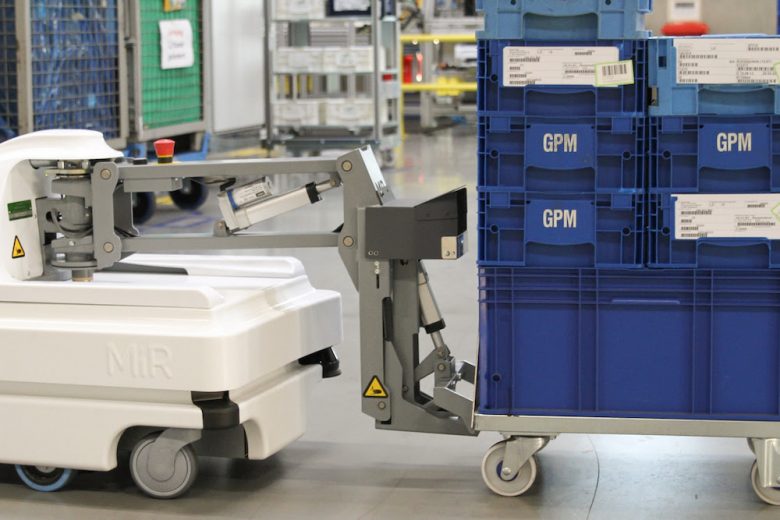
Img source: therobotreport.com
The future of mobile manipulation looks promising thanks to advances in the field of sensory technology, user interface, customized motors and end effectors. Custom motor manufacturers such as Rozum create motion cores for AMRs considering the environment and tasks they’ll be used for. The integration of these technologies will play a huge role in achieving two-dimensional motion and improves the robot’s field of vision and motion.
AMRs have also experienced the integration rollers, advanced vision, machine learning, and onboard intelligence. The integration of this technology will reduce labor costs. For instance, it takes three individuals, earning $15 an hour to unload 500 to 700 boxes within an hour. With robots, they would do it at 700 to 1000 boxes within an hour. Annually, $500,000 to $802,000 could be saved. This does not include the cost of treatment in case an accident occurs, hiring and training.
6. Autonomous Mobile Robots Will Change the World
Though the industry is young and growing rapidly, it is bound to change the world. By the next decade, it is hoped that singular use robots will have evolved into multiple-use robots. Not just that, machine to machine interaction, improved management of a large fleet, and a decentralized robot behavior should be functioning at its peak.
Currently, AMRs have reached a new milestone. It now has an outdoor application. AMR technology would be invaluable in forklift intensive operations, especially when moving cargo from trucks to loading docks.